3D Printers
At Francis Klein Aerospace Equipments, we provide state-of-the-art 3D printing solutions tailored to meet the unique needs of various industries. Whether you require high-strength metal components, durable polymer prototypes, or precision-engineered ceramic parts, our cutting-edge technology ensures superior performance, efficiency, and innovation.
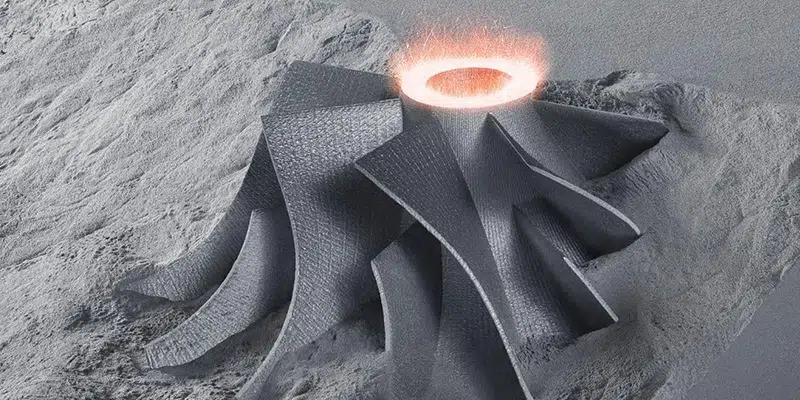
Metal 3D Printing
Our metal additive manufacturing technology utilizes Laser Powder Bed Fusion (LPBF) to produce high-strength, lightweight, and geometrically complex parts that exceed the limitations of traditional manufacturing. With advanced precision and material efficiency, our solutions are ideal for industries requiring high-performance components.
Key Features
- Technology: LPBF (Laser Powder Bed Fusion)
- Printer Range: Build volumes from 160 mm x 160 mm x 200 mm to 1500 mm x 1500 mm x 1200 mm
- Number of Lasers: 2 to 26 lasers for enhanced speed and precision
- Materials: Corrosion and heat-resistant alloys, including titanium, aluminum, stainless steel, and Inconel
- Performance: Exceptional strength-to-weight ratio for optimized efficiency
- Sustainability: Reduced lead times and material waste, ensuring cost-effective production
Applications
- Aerospace and Aviation
- Automotive
- Mold Manufacturing
- Medical
With our state-of-the-art metal 3D printing solutions, Francis Klein Aerospace Equipments empowers industries to achieve unmatched innovation, design freedom, and manufacturing efficiency.
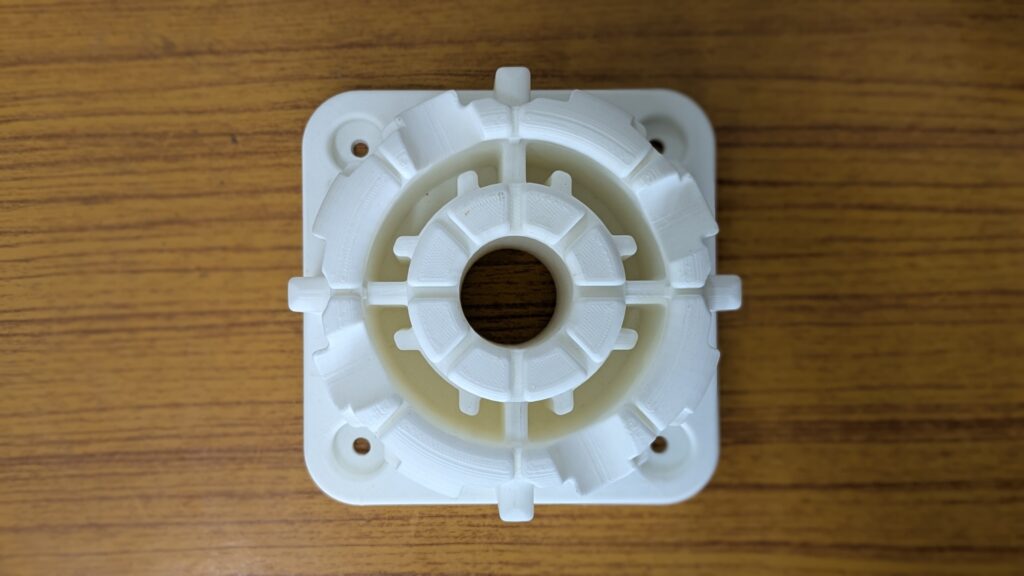
Polymer 3D Printing
Our advanced polymer 3D printing solutions utilize Fused Deposition Modeling (FDM) technology to deliver high-precision, durable, and cost-effective parts. Designed for both prototyping and end-use applications, our solutions provide exceptional versatility and reliability across industries.
Key Features
- Technology: FDM (Fused Deposition Modeling)
- Build Volumes: 420 mm x 300 mm x 220 mm to 420 mm x 300 mm x 400 mm
- Printer Options: Desktop series and industrial 3D printers available
- Materials: Open filament system allowing a wide range of thermoplastics, resins, and composites
- Surface Quality: High-quality finishes for both functional prototypes and final products
- Strength & Efficiency: Lightweight yet strong components for enhanced performance
Applications
- Consumer Goods
- Healthcare
- Automotive
- Education
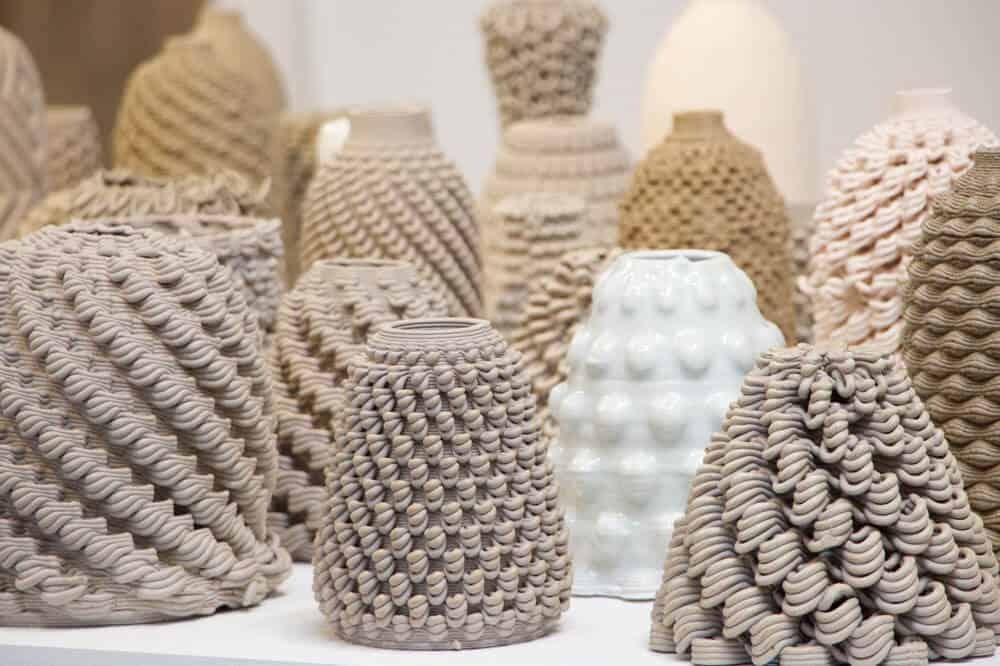
Ceramic 3D Printing
Our ceramic additive manufacturing solutions utilize MOVINGLight® DLP (Digital Light Processing) technology to produce high-precision, durable components with complex geometries. This advanced technology is ideal for applications requiring exceptional heat resistance and chemical stability.
Key Features
- Build Volumes: Capable of producing intricate parts with high accuracy
- Materials: Compatible with ceramic slurries, including silica and alumina, optimized for enhanced mechanical properties
- Surface Quality: Delivers smooth finishes suitable for functional prototypes and end-use components
- Efficiency: High-speed production with reduced material waste, ensuring cost-effective manufacturing
Applications
- Aerospace & Defense: Components requiring thermal stability and precision
- Biomedical: Biocompatible implants and surgical tools
- Electronics: Insulating parts with complex geometries
- Industrial Engineering: Wear-resistant parts for harsh environments
At Francis Klein Aerospace Equipments, we leverage cutting-edge ceramic 3D printing technology to provide innovative solutions that meet the rigorous demands of various industries.